Automatically more efficient!
Why automation?
Stronger competition, cost pressures and shortage of skilled labor are challenges companies are faced with nowadays. This is why a reasonable degree of automation seems to be mandatory, in order to increase productivity and efficiency.
Grip the future with LANG
Automation systems by LANG cover every need from single part or large-scale production. They are flexible, uncomplicated and offer best value for money. This makes them appealing for SME's and for those just starting out.
One-shift operation
(thereof 1 hour of downtime)
Downtimes
Pay off calculator
Will a RoboTrex automation system pay off for my company? Find out for yourself!
The machining hour gain using the RoboTrex automation system per year is: 1 hours
Return on investment within:
This pay-off calculation offers only a rough guide value. It is based on a RoboTrex 52 automation system with four fully equipped trolleys or a RoboTrex 96 automation system with two fully equipped trolleys. Country-specific and currency-related deviations are not taken into account. It is to be assumed that during these additional machining hours other value-adding tasks take place or that the automated machine tool operates unmanned (e.g. at night). In order to receive a specific and individual calculation, please feel free to call your LANG contact person.
Convinced by this result? Then simply use the contact form to ask for your individual quote.
Product overviewRoboTrex Automation System
Efficiency, speed and flexibility - RoboTrex combines all these attributes and prepares your manufacturing for future tasks!
RoboTrex at a glance
Efficient in every way
Off-line loading of trolleys
Quick loading of automation system
Easiest operation
Flexible and movable storage
Ideal storage capacity / required space ratio
No additional utilities necessary
Start and stop mark
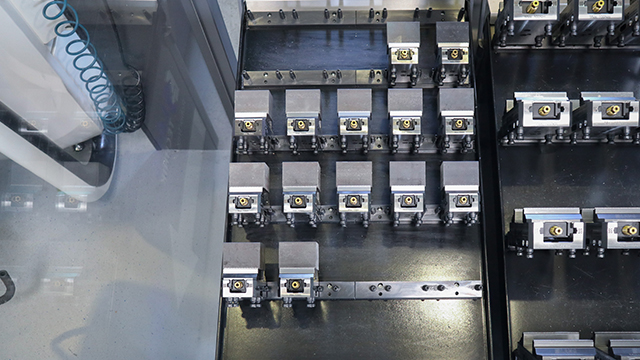
Deselection of vise positions
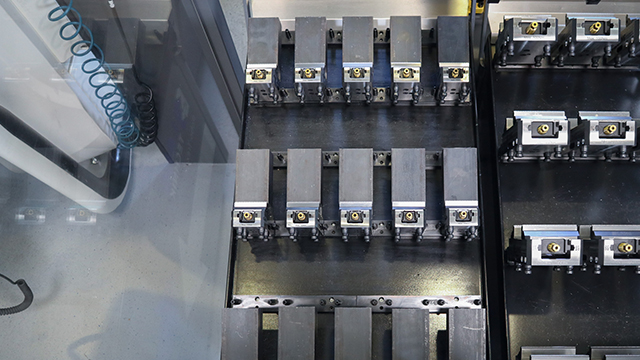
Individual program assignment
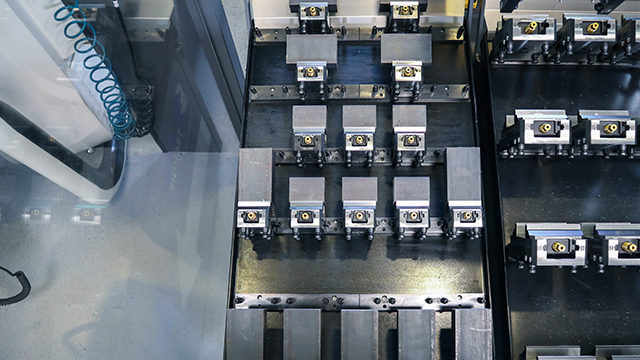
Komponenten
The Robot / gripper
Great flexibility
- Proven Fanuc quality
- Standard industrial robot with six axes
- Max. workpiece weight 12 kg (RoboTrex 52) / 25 kg or 45 kg (RoboTrex 96)
- Gripper exchange interface as standard with RoboTrex 96 allows simultaneous utilization of RoboTrex 52 components
- RoboTrex 52 zero-point device can be controlled either mechanically oder pneumatically
- Delivered in a ready-to-operate and pre-programmed state
- Equipped with a collision detection and an electronic safety fence system
The Quick•Point® Zero-Point
Clamping System
Versatile operation
- Actuated mechanically by the robot, or
- Pneumatically by the machine tool, or
- Pneumatically by an external interface
- Repeat accuracy < 0.005 mm
- Equipped with clamping studs for an easy and quick set-up
- Also suitable for manual operation
The Control
Easiest operation
- Simple, intuitive and user friendly
- Minimum training required
- Knowledge about robots not necessary
- Flexible order management (Single-part or batch production)
1. Homogeneous part selection per trolley
2. Deselection of vise positions or complete rows
3. Assignment of a NC-program for each vise position
The Clean•Tec
Chip fan
Clean and efficient
- Cleans the machine interior after the machining process
- Removes chips and coolant without the operator having to open the machine tool door
- Wings open and close automatically by switching the machine tool spindle on and off
- Doesn't require compressed air
- Design of the chip fan allows to wash workpieces and fixtures using coolant
- Called up via the machine program and selected from the tool magazine
- Compact design for space-saving storage in tool magazine
The Trolley
Center piece of the system
- Patented, angled mounting of vises
- Maximum space utilization on a small footprint
- Changeover of vises directly on the trolley
- Off-line preparation of trolleys, even at a greater distance to the machine tool
- Trolleys are exchanged within seconds and at any time, even during operation mode
- Each trolley or each vise position can be assigned to a specific machining program. Deselection of vise positions or entire rows also possible
- Interchangeable and usable on different RoboTrex systems
- Easy and unrestricted access to all vises
- Up to 4 trolleys for each RoboTrex system
- 2 trolleys with different storage capacities for each system (RoboTrex 52 and 96)
- Special vise alignment for different workpiece sizes
- Each trolley can be assigned to a specific machine program
- Trolleys not in use can remain inside the RoboTrex enclosure
Makro•Grip® 5-Axis Vise
Highest holding forces
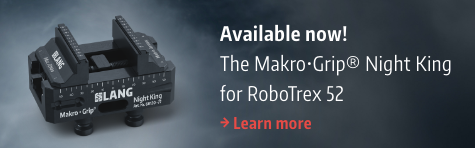
- Highest holding forces and process reliability thanks to form-closure clamping
- Best accessibility in 5-axis machining
- No wear on clamping jaws, not even when clamping harder materials
- Tremendous material savings due to minimal clamping edge requirements
- No deformation of workpieces when clamping/releasing thanks to low actuation torque
- Ergonomic handling characteristics due to compact and light-weight design
Technical data
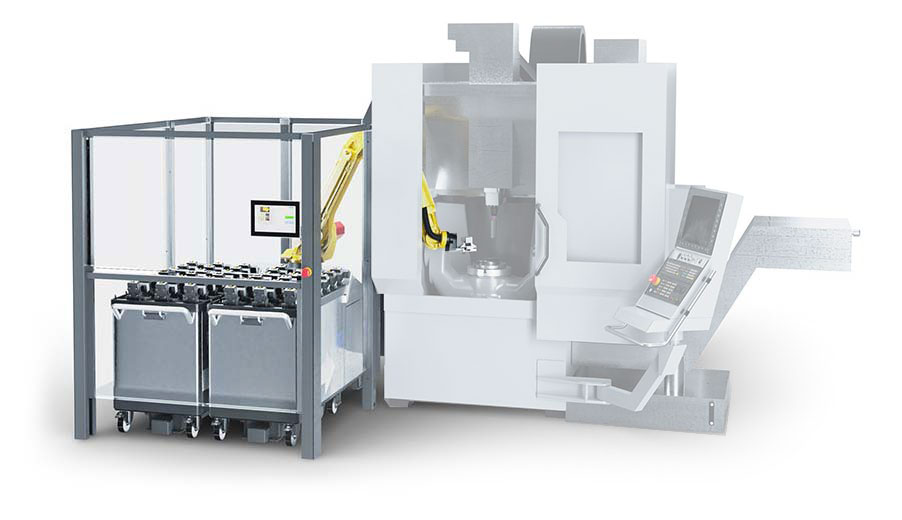
RoboTrex 52Automation System
RoboTrex 96Automation System
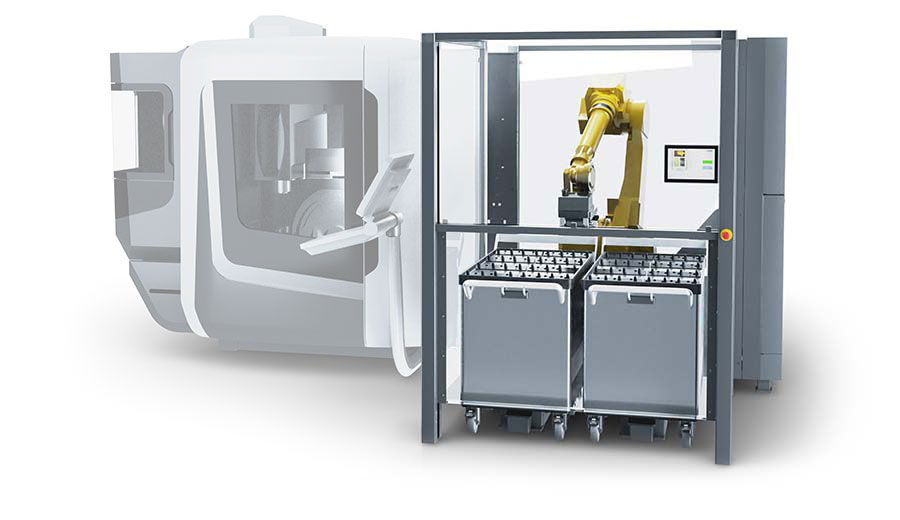
max. 120 × 100 × 70 mm
Special vise alignment allows different part dimensions
max.205 × 150 × 150 mm
Special vise alignment allows different part dimensions
optionally: max. 45 kg
RoboTrex 52 and 96 automation trolleys next to each other? The new gripper exchange interface, which comes as a standard with the RoboTrex 96 system, allows the utilization of both sizes and ensures even more flexibility in the machining process.
Technical requirements
- Almost any machine tool - whether new or already in use - can be automated with RoboTrex
- The only real requirement is a free acknowledgeable M-function or standardized automation interface
Benefits of the RoboTrex Automation
What favors the RoboTrex Automation over other palletizing and part handling systems?
Benefits of RoboTrex
over other palletizing systems
With the LANG system, vise and pallet build a compact unit. This results in high space savings in the machine, as well as a high storage capacity of the entire automation system on a small footprint
Compact vise (without additional pallet) grips workpieces which can substantially exceed the vise’s volume, whereas competing systems usually use big pallets (e.g. 400 x 400 mm) to clamp relatively small workpieces
There is no additional vise-pallet interface, which has a positive effect on stability and manufacturing accuracy
Thanks to simple communication between automation and machine tool, the installation of the RoboTrex system, which is delivered in a ready-to-operate state, is very simple and hardly time-consuming. As a result, downtimes of the machine tool can be avoided almost completely
Automation trolleys are equipped with vises off-line and location-independently. Within just a few seconds the automation system is fed with fresh trolleys and ready to machine a new batch
One-touch operation gives the operator access to the entire storage. The accessibility to each vise point is guaranteed. This allows immediate (quality) control of the finished parts even during operation
over part handling systems
RoboTrex comes with a single gripper, no matter which workpiece size or shape, no adaptation of the gripper is required for different workpieces
Thanks to the Makro•Grip® stamping technology, many compact vises can be stored on the smallest possible footprint. At the same time, the stamping technology guarantees maximum process reliability in milling
RoboTrex uses the same storage medium for all workpieces, which makes the system universally applicable even with high vertical integration
The automatic (un-)loading is independent of the milled contour, since the Makro•Grip® 5-Axis Vise is the handling interface. No problems with bulky parts
Thanks to the accuracy of the zero-point clamping system and the defined gripping contour of the Makro•Grip®, a quick and easy reproduction of the clamping situation is possible if workpieces have to be re-clamped for any necessary reworking
For manual non-automated manufacturing, the Makro•Grip® 5-Axis Vise can be used at any time in other machines, which maintains flexibility in production at all times
Write your own success story with an automation system by LANG Technik.
Product overviewSuccess Stories
Automating with RoboTrex pays off - according to our customers
RoboTrex automation is our very first investment into robotic solutions. Nevertheless it has been very easy to integrate it into our production system and to start practicing lights-out manufacturing. We have been enjoying very professional and fast customer service from LANG Technik and from its distributor in Baltic States MTC. Their customer-oriented approach has made this technology transfer very easy for us.
Tanel Joost, Equa ÖU, Tartu Estland
One of the main reasons for RoboTrex was how easy it is to use. It does not require a Profibus and is limited to the most necessary communication with the CNC machine. We now have some additional automation trolleys with Makro•Grip® and Avanti vises. It allows us to pre-equip a trolley offline which is very convenient and to change-over to a different workpiece type within the shortest time possible. It also means that smaller quantities can also be produced with this type of automation. Our positive experience with the first two systems prompted us to now integrate the third RoboTrex into our production.
Albrecht Schmid, Lindauer Dornier, 88129 Lindau
The fact that the automation system is "maintenance free" has been important and of great benefit, especially in the last year with all the limitations of Covid-19, which has left a big mark on the economy. Thanks to this investment we have not been affected as much as we would have been without the RoboTrex. The combination of a high-quality milling machine and RoboTrex was the best investment the company has ever made.
Jonas Sivertsen, Induform AS, Levanger Norwegen
In our 2-man-operation it often happened in the past that we had to work well into the night to be able to meet critical deadlines. By automating one of our machines with RoboTrex we are now able to use our existing capacities more efficiently to increase our productivity. RoboTrex is the ideal solution for our range of products which largely consists of rather small aluminium components. Besides the functionality of the system, another thing that impressed us was the fast and uncomplicated service from LANG. The technician made adjustments on site in the shortest time possible and we were very satisfied with the communication.
Georg Spiel, Clemens Spiel Präzisionsmechanik, 83052 Bruckmühl
By using the RoboTrex automation system we were able to generate an incredible number of additional machining hours. In some cases, our machining centers run for over 200 hours without any downtime. In our 5-axis area, six of seven machines are currently automated with LANG and all RoboTrex automations are systems with 4 trolleys. This adds up to a considerable quantity with appoximately 600 vises. Thanks to the Makro•Grip® form-closure technology we often push them to the limit of what is feasible in terms of the workpieces dimensions.
Peter und Julian Klein, PJK Feinmechanik, 53757 Sankt Augustin
In order to organise the process safety of unmanned production, new tasks have been created for the team. The employees plan and secure the production. Automation makes it possible for the employee to take care of more things than inserting parts. In addition, scheduling reliability has improved and the quantity of parts has increased by almost 50 % due to planning security.
Heiko Blochwitz, Mechanische Werkstätten Blochwitz GmbH & Co. KG, 09326 Geringswalde
The key to profitability is a productive night shift without operators being present. With minimum effort we were able to make better use of our machine capacities and as a result increased our productivity tremendously. In less than a year the practical solutions by LANG Technik were amortized.
Simon Oreskovic, Zelos Zerspanung, 63856 Bessenbach
RoboTrex applications
From our blog
You can find more detailed information and application examples in our blog
Are you ready to make your production more efficient?
Product overviewLearn more about other solutions by LANG
Quick•Point® Zero-Point Clamping System
Flexible, precise and extremely durable – with the modular Quick•Point® system set-up times are reduced to a minimum.
More detailsQuick•Point® Rail quick clamping system
Maximum efficiency with minimum use of resources - the revolutionary quick-clamping system for all machine tables and automation pallets in the CNC milling sector.
More detailsMakro•Grip® Raw Part Clamping and Stamping Technology
Clamping parts by form-closure – For years the Makro•Grip® technology has been the benchmark in the 5-axis machining of raw material.
More detailsHAUBEX Automation System
HAUBEX enables the automatic exchange of the workholding device from the tool magazine with a hood as a carrier system for the vise and workpiece blank.
Learn moreMakro•Grip® Ultra
The modular workholding system is characterized by an enormous application variety and is ideally suited for clamping plates and large parts.
More detailsConventional Workholding
Conventional Workholding offers flexible and versatile solutions for clamping round or pre-machined components and contours.
More detailsClean•Tec Chip Fan
The chip fan automatically removes chips and coolant from machine tables, fixtures and workpieces after the machining process.
More detailsQuick•Point® Zero-Point Clamping System
Flexible, precise and extremely durable – with the modular Quick•Point® system set-up times are reduced to a minimum.
More detailsQuick•Point® Rail quick clamping system
Maximum efficiency with minimum use of resources - the revolutionary quick-clamping system for all machine tables and automation pallets in the CNC milling sector.
More detailsMakro•Grip® Raw Part Clamping and Stamping Technology
Clamping parts by form-closure – For years the Makro•Grip® technology has been the benchmark in the 5-axis machining of raw material.
More detailsHAUBEX Automation System
HAUBEX enables the automatic exchange of the workholding device from the tool magazine with a hood as a carrier system for the vise and workpiece blank.
Learn moreMakro•Grip® Ultra
The modular workholding system is characterized by an enormous application variety and is ideally suited for clamping plates and large parts.
More detailsConventional Workholding
Conventional Workholding offers flexible and versatile solutions for clamping round or pre-machined components and contours.
More detailsClean•Tec Chip Fan
The chip fan automatically removes chips and coolant from machine tables, fixtures and workpieces after the machining process.
More detailsQuick•Point® Zero-Point Clamping System
Flexible, precise and extremely durable – with the modular Quick•Point® system set-up times are reduced to a minimum.
More detailsQuick•Point® Rail quick clamping system
Maximum efficiency with minimum use of resources - the revolutionary quick-clamping system for all machine tables and automation pallets in the CNC milling sector.
More detailsMakro•Grip® Raw Part Clamping and Stamping Technology
Clamping parts by form-closure – For years the Makro•Grip® technology has been the benchmark in the 5-axis machining of raw material.
More detailsHAUBEX Automation System
HAUBEX enables the automatic exchange of the workholding device from the tool magazine with a hood as a carrier system for the vise and workpiece blank.
Learn moreMakro•Grip® Ultra
The modular workholding system is characterized by an enormous application variety and is ideally suited for clamping plates and large parts.
More detailsConventional Workholding
Conventional Workholding offers flexible and versatile solutions for clamping round or pre-machined components and contours.
More detailsClean•Tec Chip Fan
The chip fan automatically removes chips and coolant from machine tables, fixtures and workpieces after the machining process.
More details