A workholding system in new dimensions
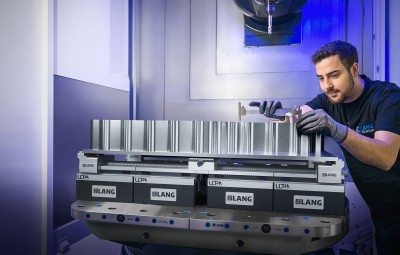
Machining plates and large components with Makro•Grip® Ultra
At the end of October, Lang Technik announced big news in the truest sense of the word. Having already launched a number of innovations in the first half of the year, the Swabian workholding and automation expert released Makro•Grip® Ultra, a completely new workholding system designed for plates and large-part clamping as well as applications in mould making. As the name suggests, this system is based on the proven Makro•Grip® series, which has been the reference in 5-sided machining of blanks for many years. Features such as the form-fit clamping principle were adopted and combined with the advantages of the company's own zero-point system. The result is a new type of workholding system that is even larger, more flexible and more modular than the solutions previously known from Lang and, according to the company's own information, is a system that can cover practically every machining application imagineable in the range up to approximately 800 mm.
This becomes particularly clear when taking a closer look at the modular system. In a total of three different system heights, the base bodies of the workholding system can be combined and connected with each other as desired in the 96 mm grid of the zero-point clamping system. This not only makes it possible to extend the system, but also to expand it in the y-direction with additional clamping units for wider workpieces and plates. By default, Makro•Grip® Ultra is designed for maximum clamping ranges of 410, 610 and 810 mm. Depending on the size of the machine table and its equipment with zero-point plates, longer clamping ranges can also be realised with a customized spindle.
For the actual workpiece clamping, the operator has several options and clamping jaw types at his disposal. Depending on the requirements of the component, a choice can be made between serrated jaws, individually machineable top jaws or hardened clamping jaws with a plain clamping step. All clamping jaw types feature an innovative quick-change mechanism, which has a positive effect on the time required for setting up the system or removing it and, thanks to variable jaw positioning, also enables the clamping of asymmetrical components. Flexible mounting options in the system centre allow switching between centric single-part and compensating multiple clamping.
A matter of course for Lang with this system was the development of a size-matching stamping system. "Due to the achievable holding forces and process reliability through pre-stamping, it was no question for us to further develop the stamping technology for the new system. Particularly with large components and flat and deformation-sensitive material, these advantages pay off even more," says Wolfgang Suchy, project manager for the development of Makro•Grip® Ultra, adding that the stamping technology ideally rounds off a coherent workholding system.
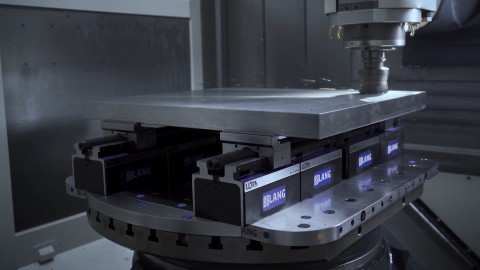
This video is hosted on YouTube. To watch the video please accept the media cookies in the privacy settings.
Learn more about Makro•Grip® Ultra.
Go to Product Solutions