Instagram Q & A #1 - we answer your questions!
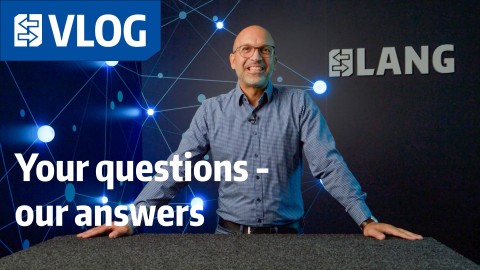
This video is hosted on YouTube. To watch the video please accept the media cookies in the privacy settings.
What are your thoughts on: Vise with fixed jaw vs. centering vise?
As always, there are points that speak for and against. A machining vise with a fixed jaw usually takes away some accessibility due to the design. One side is long, the other short, which is rather unfavorable for 5-axis machining. On the other hand, you always have a reference point for this, which needs to be set only once. Every clamping device tends to tilt slightly at the loose jaw. This means that, in the worst case, one side of the vise with fixed jaw goes up. With the centering vise, best case scenario would be that both sides lift equally, which creates a certain flatness. For me, both types have their right to exist. The machine type – for instance 3- or 5-axis machine, the workpiece dimensions, or the clamping options are the parameters that lead to the right decision.
What are the benefits of pre-stamping?
By pre-stamping the workpiece with a stamping unit outside of the machine, you no longer have the need to apply large clamping forces with the clamping device in the machine, as the workpiece is held by form-fit in the serration of the vise. With a compact vise you achieve highest holding forces due to the form-fit and the best accessibility. A dream for every machinist. There is also no deformation of the workpieces due to the low clamping forces during machining. In addition, a small stock allowance is required, since we clamp on just 3 mm. In other words this means: Less material costs and less material to mill off the 6th side. Re-clamping of the workpiece in case of a potential rework is possible with an accuracy of a few hundredths of a millimeter, because of the defined imprint in the pre-stamped workpiece. For further details, please visit our website or contact us if you would like to test the stamping system in your production together with the clamping device.
Will there be higher Profilo top jaws in the future?
We have chosen the current jaw dimensions, because we think that with this size you are able to cover most applications. The nice thing about the Profilo system is that you can manufacture your own top jaws, tailored to your own needs. We are also happy to offer special jaws for orders of 10 pairs or more. If you are interested, please send us an inquiry or talk to your contact person at LANG or to an official LANG distributor.
A service technician said, he doesn't like the Clean•Tec fan, because it spreads chips everywhere.
Well, the aim here is to clean the workpiece after machining so that there is no carryover of chips and coolant. Especially with an automated machine. To accomplish that, the chips have to go somewhere else. I think the machine interior is more suitable than the production hall. A small program can be used here to ensure that it can be cleaned in a more targeted way. The most common method here is to tilt the table and simultaneously rotate it during the cleaning process.
How many automation systems do you have installed worldwide?
There are now 800 automations worldwide. Almost half of them are RoboTrex systems. An interesting fact: Many customers are repeaters. In other words, once RoboTrex is up and running in a machine shop, customers often follow up with another system. For us, this is the best proof of customer satisfaction.
Currently we have nothing planned here in this pallet size. But - never say never. However, upon request and inquiry, we offer our customers the possibility to purchase special pallets for the RoboTrex automation. These pallets are zero point pallets with integrated robot interface. Fixtures or vises can then be mounted on these pallets to clamp components up to a size of 400 mm, for example.
Do you have a surprise in store for EMO?
In fact, at EMO we will be presenting new products for each area - automation, zero point clamping and workholding technology, that will make your manufacturing processes more flexible and efficient. Just stop by in Hall 3 in September, you are very welcome!
What is the difference between the Makro•Grip® and Night King vise?
The Makro•Grip® is our all-rounder. This vise has everything you need for any clamping application, thanks to the wide variety of jaw types and the finished surfaces. The Night King however is a pure raw part vise. Here, the focus is really on machining a workpiece blank from the solid block and if possible, in one clamping operation. Particularly in automated manufacturing, where many vises are utilized, the necessary clamping device can be used depending on the task. Accordingly, the costs are also lower and everything is tailor-made.
Here, we are referring to the combination of a zero point plate and a vise. However, the figure is actually no longer up-to-date. We are now at over 20,000 zero point plates and over 30,000 centering vises per year.
You should bring backt the small Makro•Grip® 46 vise.
We never really pulled it from the product range. The demand was just too high for that. It was still available through our special item department and you can also find it on our website. I think there's still a big little surprise waiting in this area in particular at EMO. Stay tuned.